Products
Thank you! Your submission has been received!
Oops! Something went wrong while submitting the form.
XX products
Tag
Close Filters
Top Level, Fast response, spectrally flat, Class A Pyranometer that meets the strict standards of ISO 9060:2018
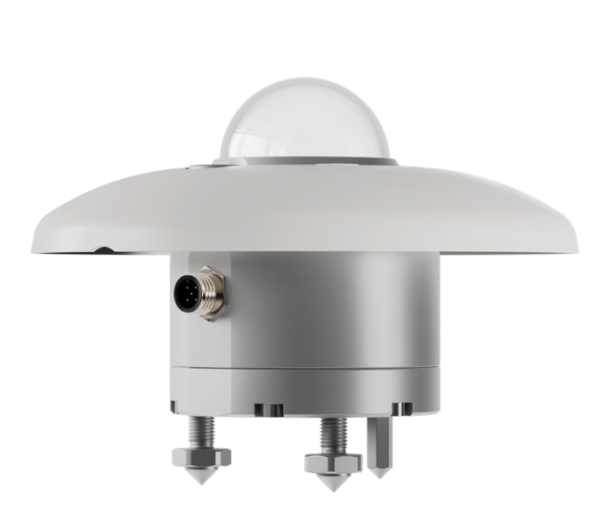
Pyranometers
Class A Fast Response Pyranometer
PYRAsense - LPR10M0T
Robust dual channel professional grade handheld
meters for thermocouple probes.
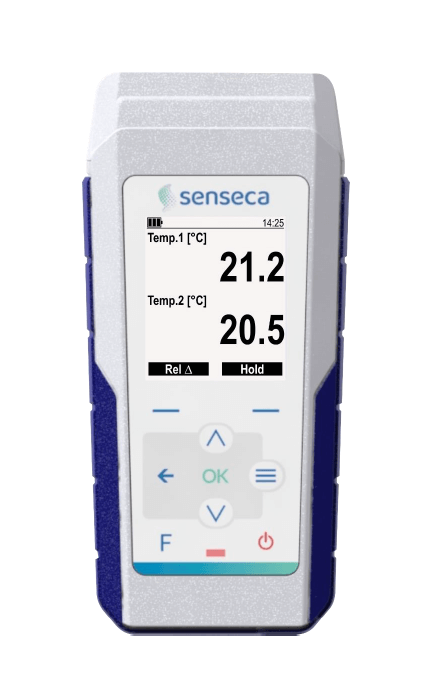
Temperature
2-Channel Thermocouple Meter / Data Logger
PRO131.2 | PRO 135.2 (Data Logging
AX 111 are precision analog Pt100 temperature probes based on thin film sensor technology.
AX 115 are high precision analog immersion probes incorporating wire wound Pt100 sensors for best precision.
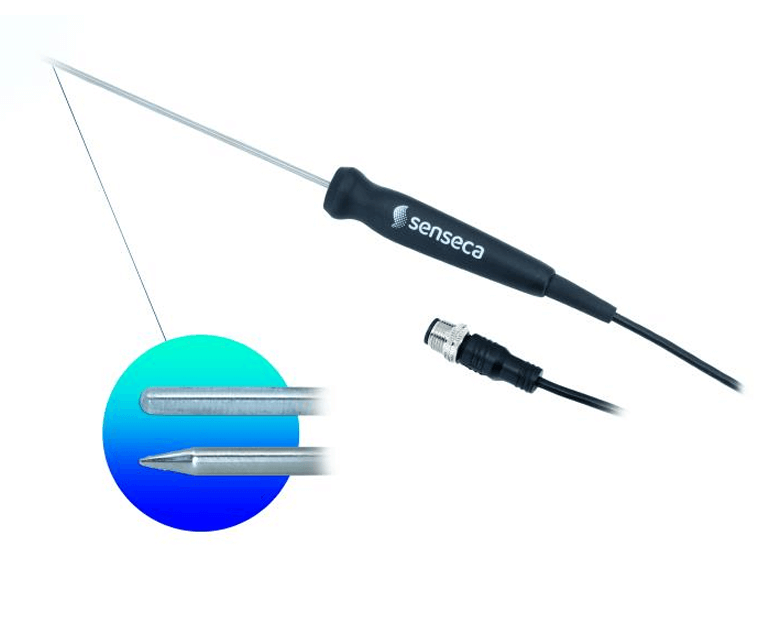
Temperature
Pt100 Precision 4-wire Probes
AX 111 | AX 115
PRO 111 and PRO 115 are high class professional handheld meters for 4-wire Pt100 probes with a rich set of features, high grade robustness and operating comfort for safe and reliable use.
PRO 115 also has data logging capability.
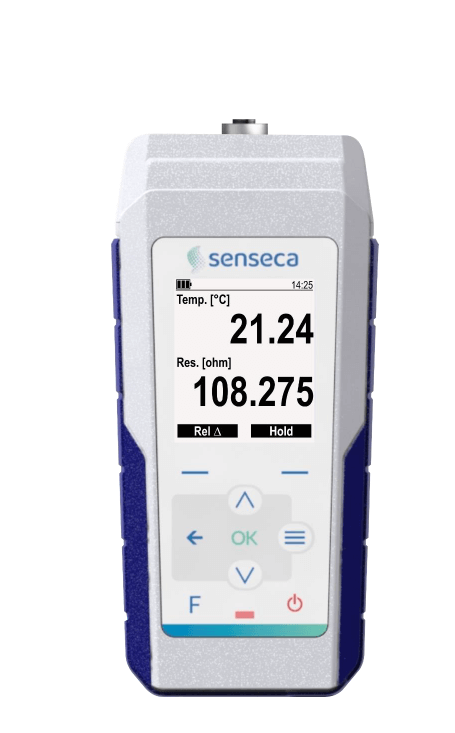
Temperature
Professional Pt100 4-wire high precision thermometer
PRO 111 | PRO 115
2 or 4 input data logger covering universal analog or digital inputs.
.png)
Multiparameter Data Logger
Analog / Digital Data logger with color touch screen
CMC-N16
AISI-316L Stainless Steel fixed switch point level switch with armored cable. RINA Naval and Exia Atex Certified
Level Switch
Stainless Steel Simple Bilge Level Switch
SIMPLE BILGE
Environmental temperature, relative humidity and, optionally, barometric pressure transmitter with standard RS485 Modbus-RTU / Analog output.
Temperature
Temperature, Relative Humidity & Barometric Pressure Transmitter
ENVIROsense
High-speed isolator provides signal output which is isolated between input, output and power-supply.
Isolator
High Speed Response Isolator
WSPF-DE
Compact plug-in type converter provides 2 signal outputs which are mutually isolated between input, output and power-supply. It amplifies and converts various kinds of signal with isolation.
Isolator
Dual Output Isolator
WSPF-DSW
This expanded range compact plug-in type converter provides signal output which is mutually isolated between input, output and power-supply.
Isolator
Advanced DC Voltage / Current Isolator
WSPF-DS
DC voltage or current isolator amplifies and converts with signal isolation, highly effective countermeasure to signal noise
Isolator
Basic DC Current / Voltage Isolator
WSPF-IS
Maximize data accuracy with the new Spectrally Flat Class A albedometer
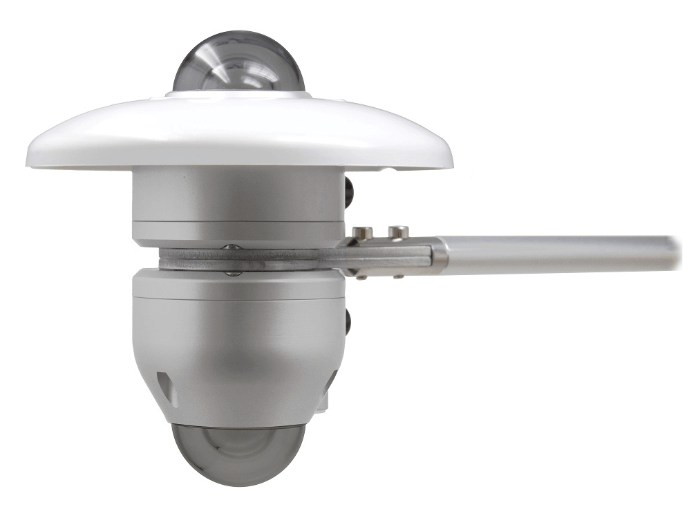
Light / Radiation
Spectrally Flat Class A Albedometer
LPS110P0
2-axis ultrasonic static anemometer - high sensitivity to detect very low speeds. Measurement of wind direction, wind speed and wind gust.
Air Speed
High Sensitivity Anemometer for Very Low Wind Speeds
HD53LS
Robust AISI 316 stainless steel low profile 3-Axial ultrasonic anemometer with integrated heating and barometric pressure sensor.
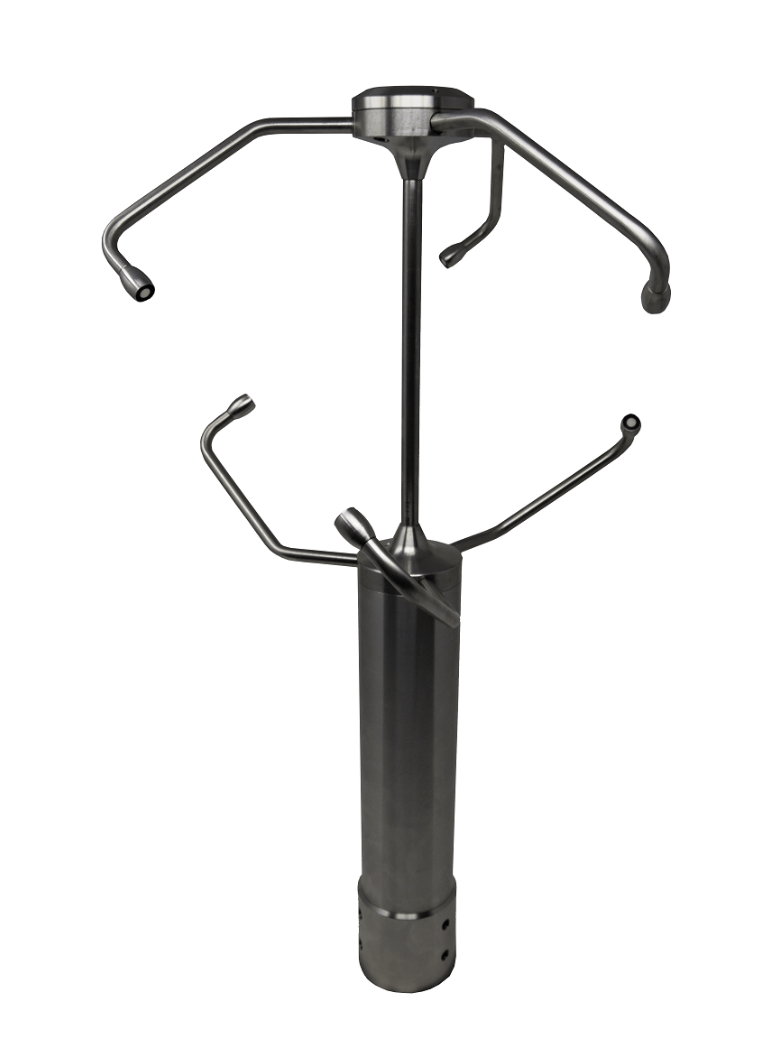
Air Speed
AEOLUS-3 Axis Ultrasonic Anemometer
WUS30FA / WUS30FW / WUS30FX / WUS30FY
The radiometric probe LP BLUE RS-USB measures the irradiance (W/m2) in the spectral range of Blue light.
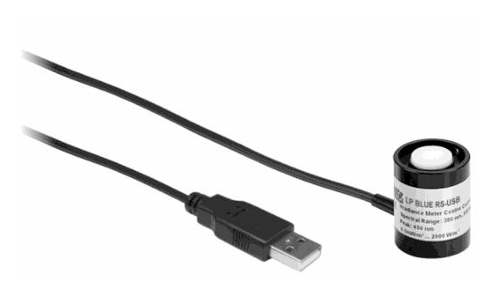
Light / Radiation
Probe for Measuring Blue light with USB Output
LP BLUE RS-USB
Personnel monitor, 0 to 1,000ppm carbon monoxide with integrated audible alarms.
.png)
Gas Monitors
Portable Carbon Monoxide Meter with Alarm
GCO100
Extremely high resolution professional manometers.
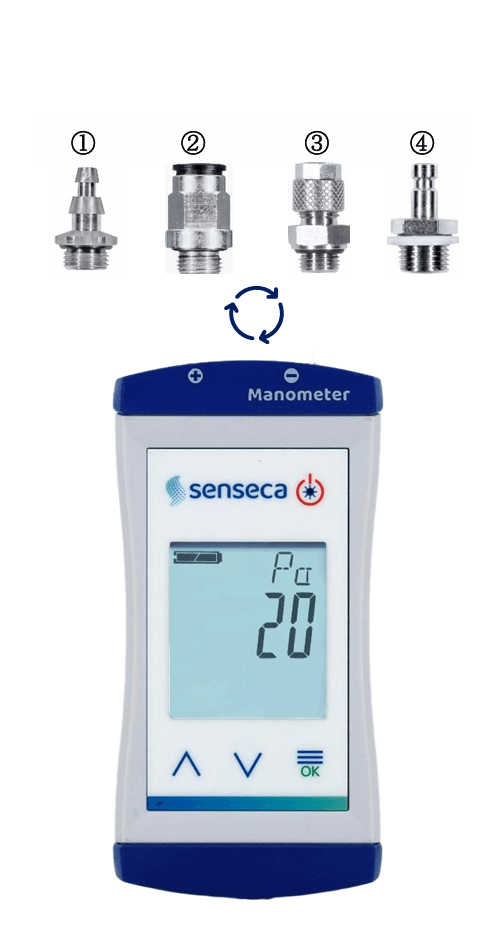
Pressure
Handheld Fine Manometer / Manometer
ECO 210-3 | ECO 210-5
J, K, or S type thermocouple input, scalable voltage or current output 0/2 to 10V or 0/4 to 20mA
.png)
Temperature
Thermocouple Transmitter Type J, K , S
TC500
Measures sunshine duration that exceeds the WMO-defined threshold of 120 W/m² and direct solar radiation 0 -2,000 W/m²
.png)
Light / Radiation
Sunshine Duration Sensor
LPSD18.1 / LPSD18.2 / LPSD18.3
Waterproof, high 0.01°C resolution, 1.1mm diameter probe, high precision calibration at 37°C as reference for medical devices in the field of IVF.
.png)
Temperature
High Precision Reference Thermometer with Micro-Probe
G1781
Thermal profile temperature probe designed in accordance with the WMO for agriculture and geothermic studies, 7 discreet depths of measurement via pt100 sensors.
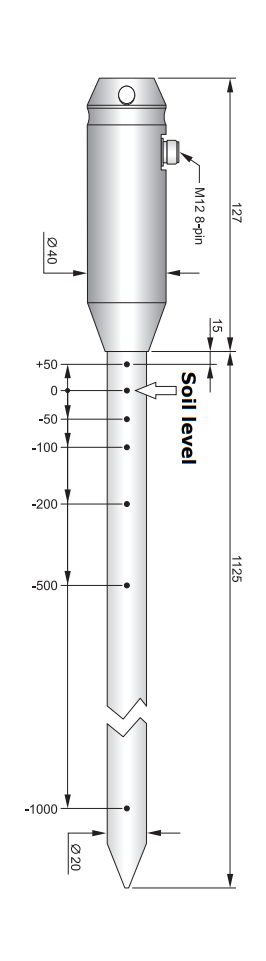
Temperature
Muli-Depth Soil Temperature Probe
TP32MTT.03 / TP32MTT.03.1
RS485 and optional voltage or current analog output, 300 to 1100 hPa.
.png)
Pressure
Barometric Pressure Transmitter - RS485 & Analog Output
BAROsense
Measures relative and absolute pressure and converts the signal to analog current or voltage. Includes programmable alarm outputs.
.png)
Pressure
Pressure Meter & Converter
UNICON-P
Measure wind speed up to 85m/s. Add temperature, relative humidity, atmospheric pressure, solar radiation, or an internal heater to create a fully functional automatic weather station.
Air Speed
High Performance 2 Axis Ultrasonic Anemometer
HD51.3D
Single or dual input thermocouple meter for type K sensors, the meter fits in the palm of your hand and responds fast with its 3 measurements per second sampling rate.

Temperature
Compact Quick Response Thermocouple Meter: Type K Sensors
G1200 | G1202
Pack of (4) 20cm wide chart paper x 15m long for Ross Chart Recorders model 201 and 202.

Chart Recorders
20cm Chart Recorder Paper
1101
Pack of (4) 10cm wide chart paper x 15m long for Ross Chart Recorders model 101 and 102.

Chart Recorders
10cm Chart Recorder Paper
1101
Non-glass Electrochemistry probe for pH, ORP, and conductivity. The probes are based on ISFET technology, and come Bluetooth enabled.
These are replacement probes for the wireless module (not included).
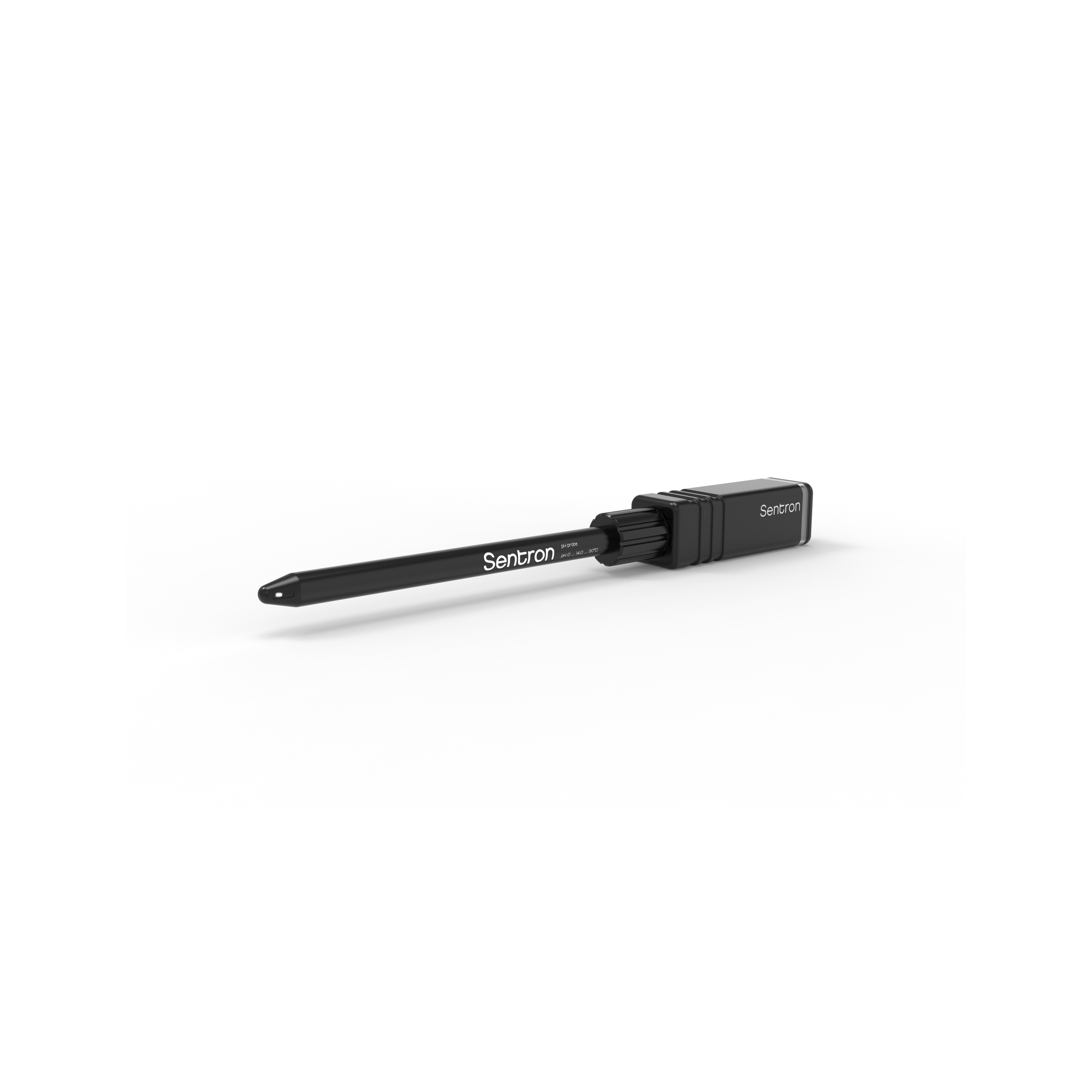
PH Measurement
Replacement Probes: Combined pH, ORP, Conductivity, and Temperature probe.
3380-205 | 2370-205
Non-glass Electrochemistry probe for pH, ORP, and conductivity. The probes are based on ISFET technology, and come Bluetooth enabled.
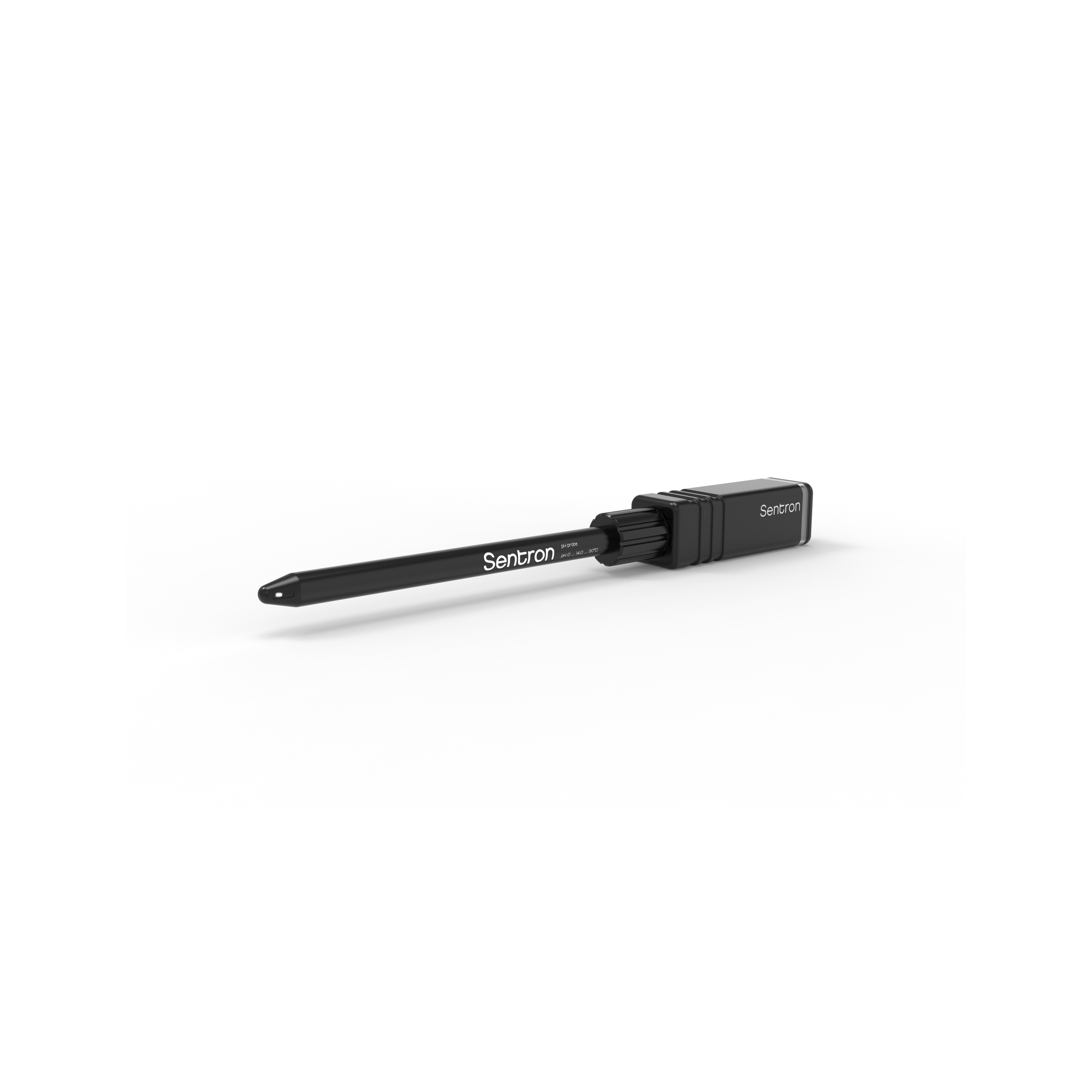
PH Measurement
Solid State Combined pH, ORP, Conductivity, and Temperature probe.
3380-205 | 2370-205
Wired replacement pH non-glass pH probes based on ISFET technology, for use with SI400 and SI600 pH meters
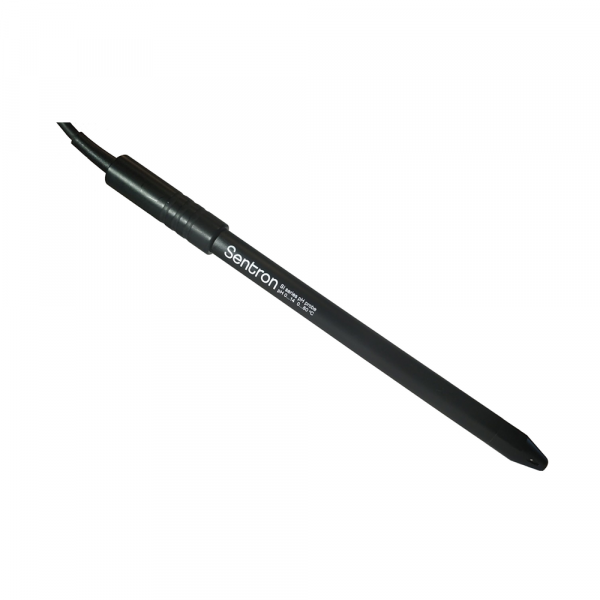
PH Measurement
Legacy ISFET pH Probes for use with SI400 and SI600 meters
Legacy ISFET wired probes
Non-glass pH probes based on ISFET technology, Bluetooth enabled. Includes a wireless ISFET probe of your choosing, rugged carry case, tablet with rugged case, screen protector, stand, and initial buffer set.
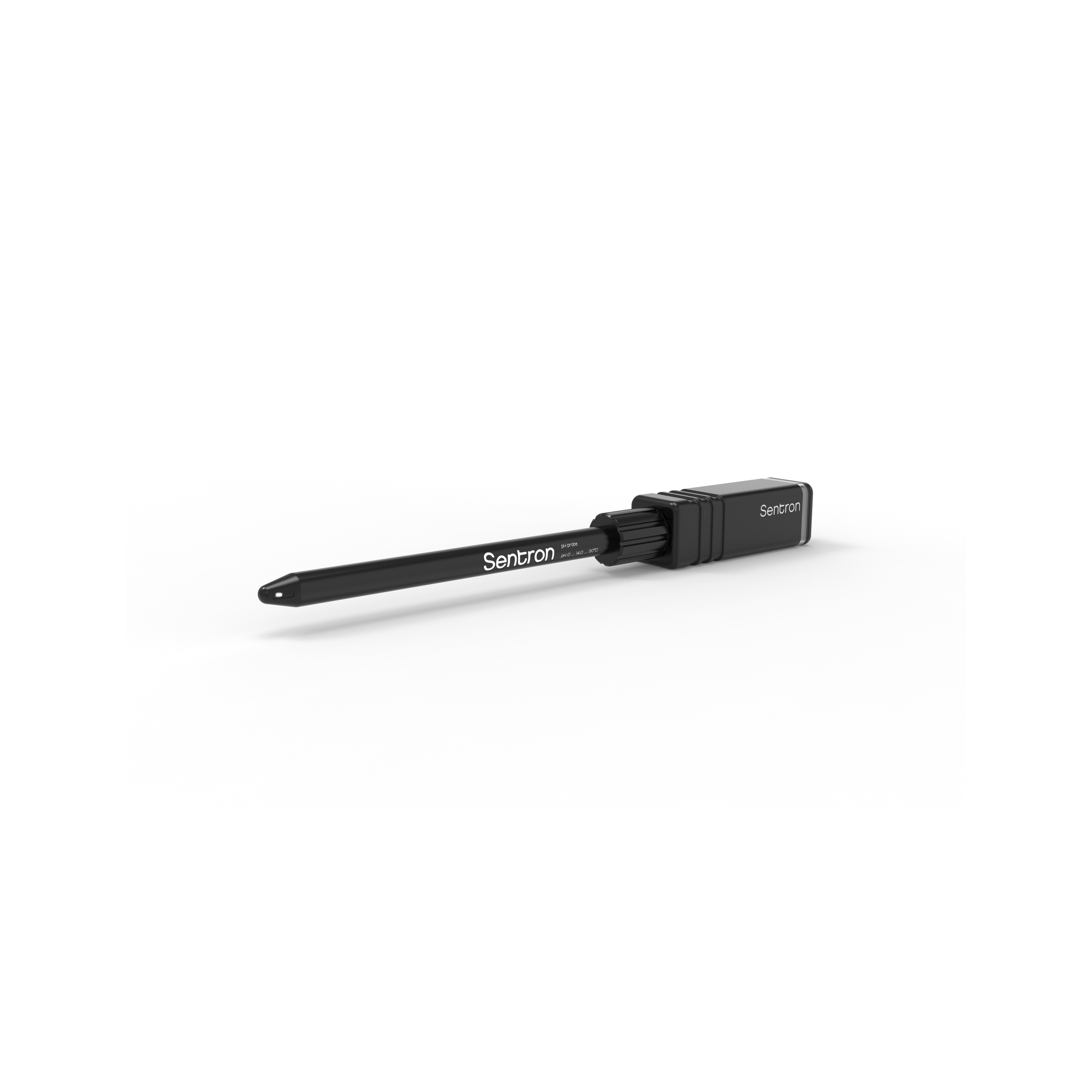
PH Measurement
Agriculture Package: Wireless ISFET pH Kit
Agriculture Kit
Non-glass pH probes based on ISFET technology, Bluetooth enabled. Includes a wireless ISFET probe of your choosing, rugged carry case, tablet with screen protector and stand, and initial buffer set.
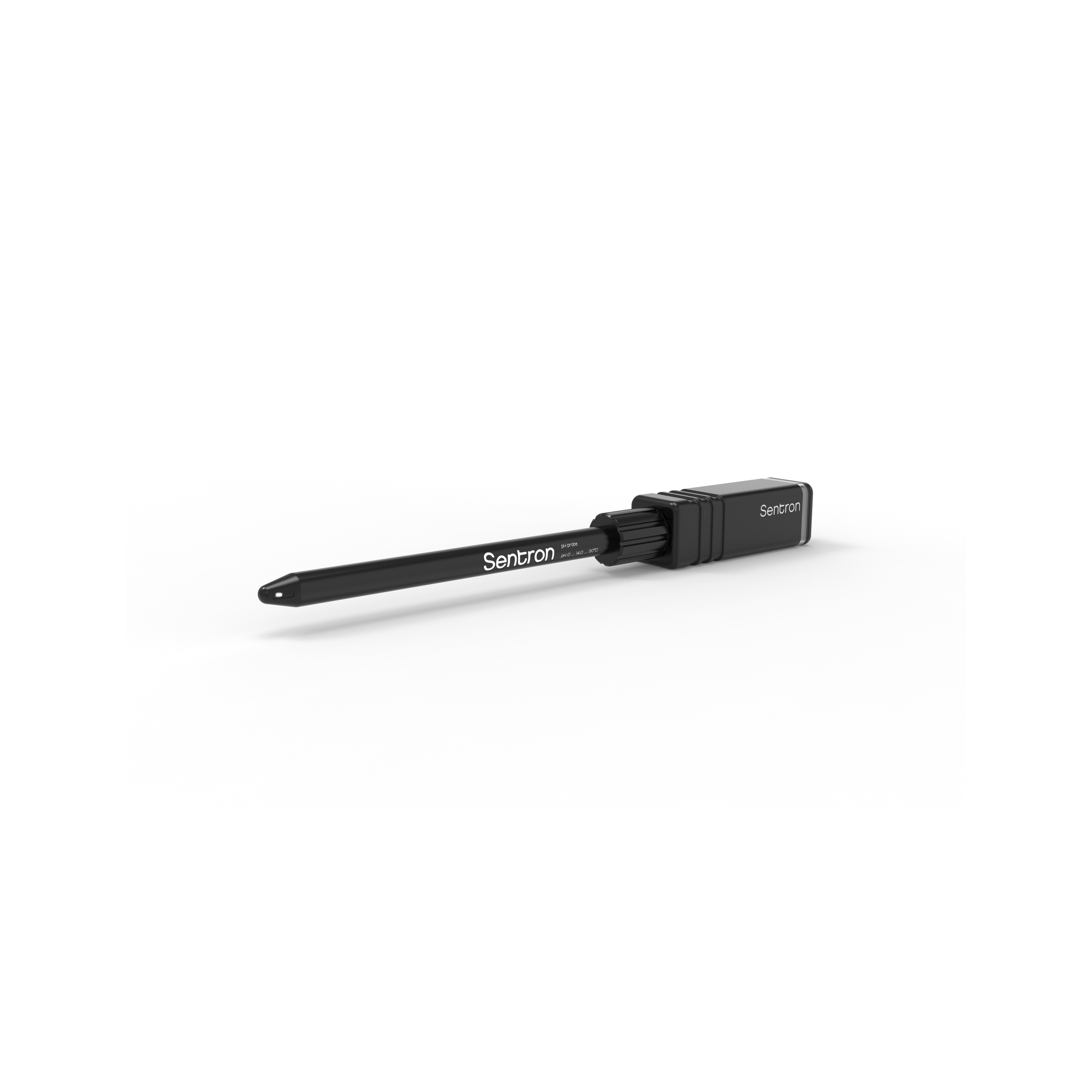
PH Measurement
Industrial Package: Wireless ISFET pH Kit
Industrial Kit
Non-glass pH probes based on ISFET technology, bluetooth enabled. Includes a wireless ISFET probe of your choosing, tablet with screen protector and stand, and initial buffer set.
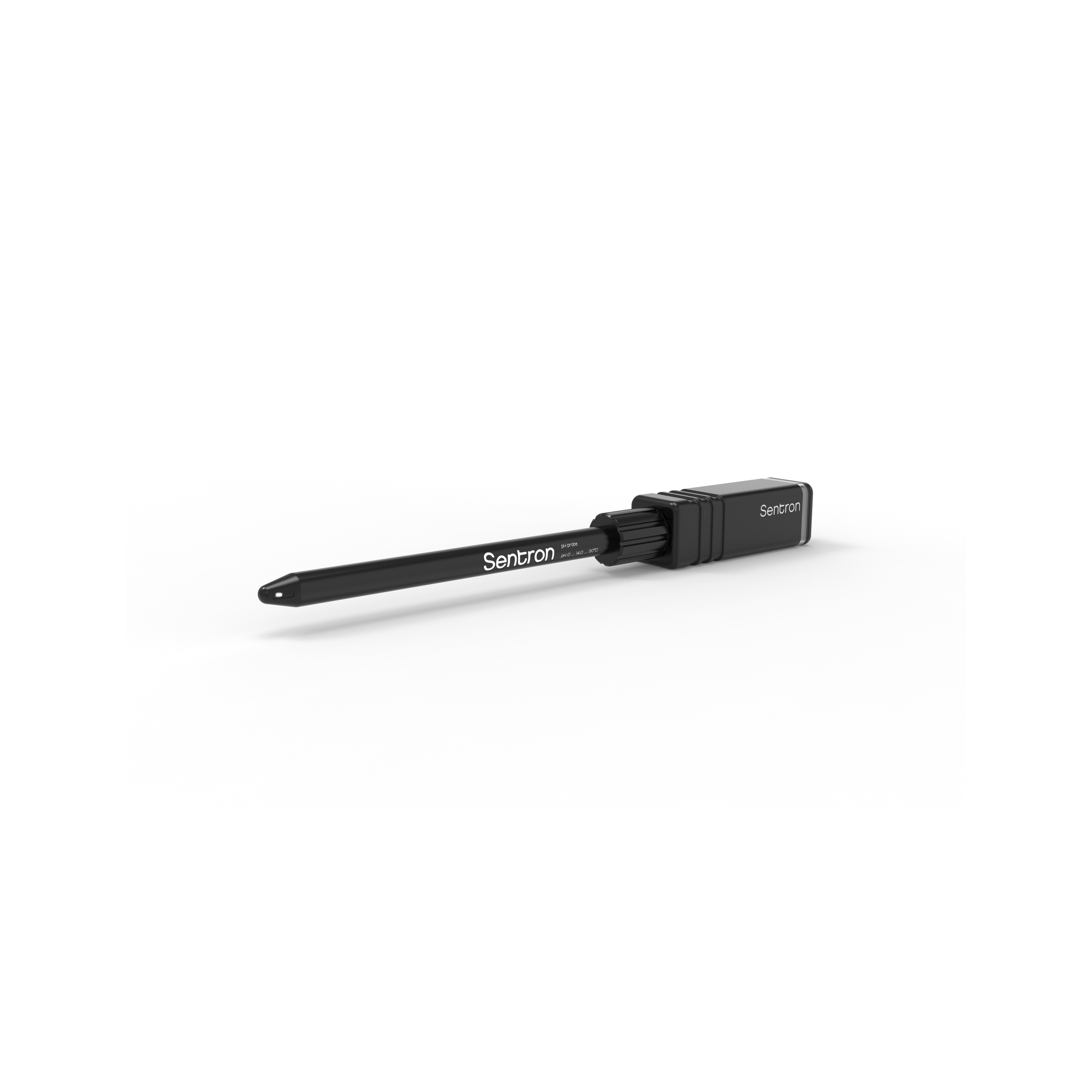
PH Measurement
Laboratory Package: Wireless ISFET pH Kit
Lab Kit
Replacement Non-glass pH probes for use with the Bluetooth module.
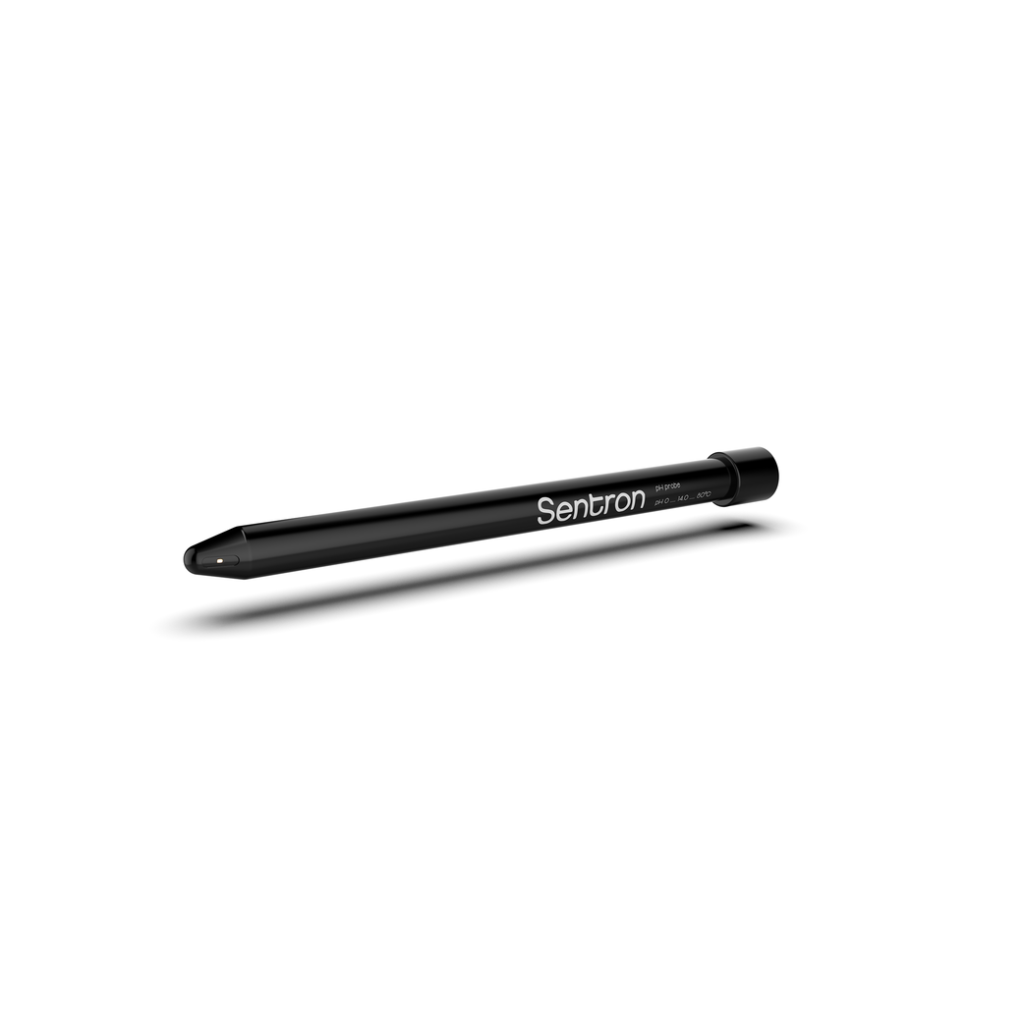
PH Measurement
Replacement Wireless ISFET pH probes
Wireless Replacement Probes
Non-glass pH probes based on ISFET technology, bluetooth enabled.
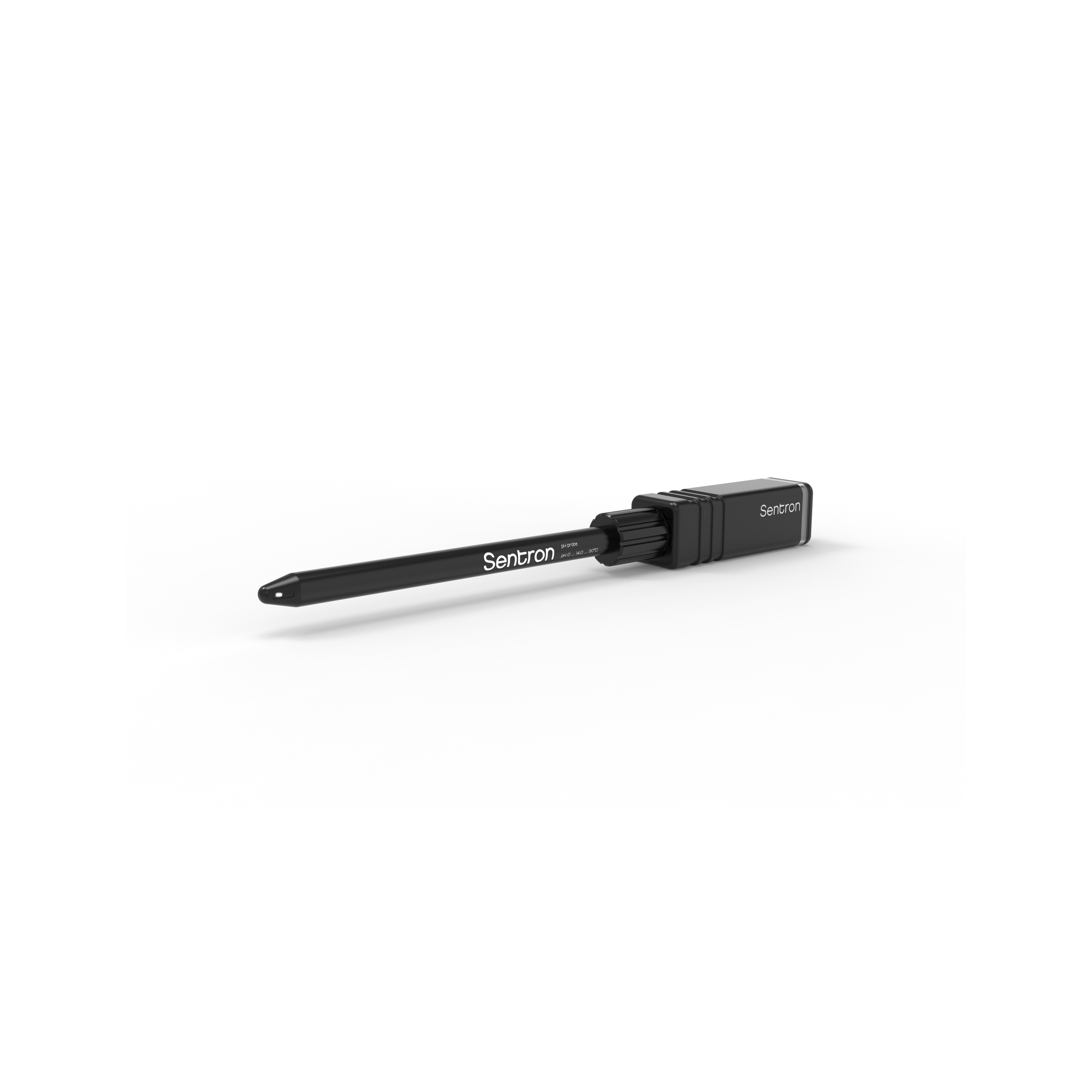
PH Measurement
ISFET pH Module+Probes
3380-100 | 3320-100 | 2370-100 | 9370-100
The G 1690 is precision gas meter, common applications are diving gas and other protective gas measurements.
Oxygen Analyzer
Compact Oxygen Analyzer
G1690